These has a few major advantages.
1. No need greasing of gears , thus cutting down maintenance time of cleaning the gears.
2. Eliminate slop and increasing backlash on the gears as they wear , and as it develops slop, the wear increases exponentially as the impact on the gears increases. with the tensioned belt drive there will be no slop internally.
3. The whole driveline will be much less sensitive to dirt ingestion, since there is no sticky grease in the gearbox.
Disadvantage
1. Since the belt needs to be tensioned tightly there will be some loss of efficiency.
Ok, I got a machinist to make up a twin belt ball diff for me and 13t top pulley, but the first iteration was a failure, because the belt skipped of the pulleys. I thought only the new fine pitch belt sklipped but in fact it was both the fine pitch and the Mid belt slipped, because the 13T pulley was too small and the profile was cut incorrectly. I later found out the technical reference for the pulley tooth dimensions were wrong causing the belt to not engage completely with the tooth, most of this is caused by the inner bottom radius on the tooth being too large.
To cut a long story short, after a lot of testing I finally got a tooth profile that works for both the original mid belt and the new short belt. I am still not entirely happy with the tooth profile and i intend to improve the profile for a bit more clearance for the production runs.
I decided to make my pulleys with shapeways as they are much quicker and cheaper than my machinist, however i do have some shirnkage issues with the smallest diff outdrive holes on the diff cases.
1. Shown below is the second version of my design, its a LA-1 pulley matched to my own designed Mid XL belt pulley, you can see the slip marks on the Mid pulley becuase the tooth profile is not quite right. I used LA-1 to isolate which side the slipping was coming from.
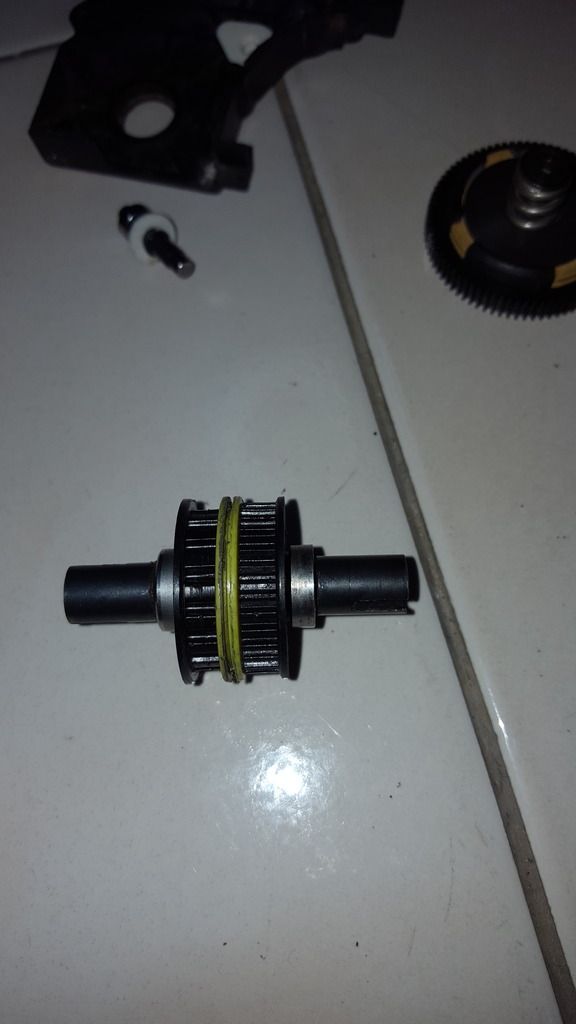
2. This is the upper pulley which is now 14T, made by 3racing but machined minorly by my brother to enlarge the inner hole from 4mm to 5mm and to make a 2mm slot on the pulley hub, to lock it down like OT86. A 3D printed insert keeps the pin from falling out.
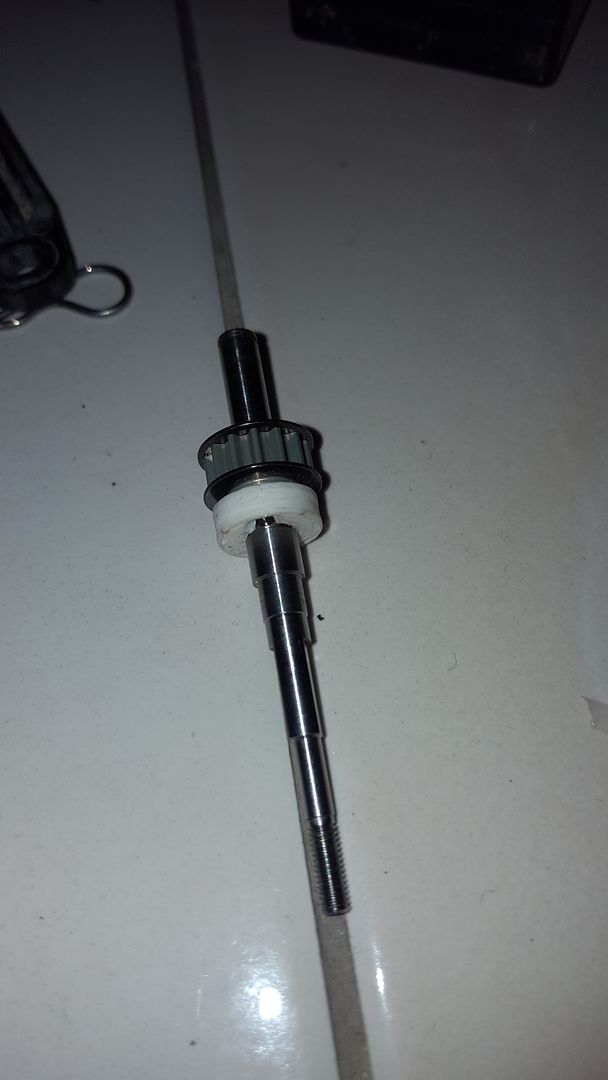
3. The original center gear position cannot be used for the most suitable belt length, so a hole must be drilled( i used a 3D printed jig to dill this new 8mm hole, and i made a offset insert to place the center gear shaft. This insert will be available in many different offsets to cater for tension adjustment.
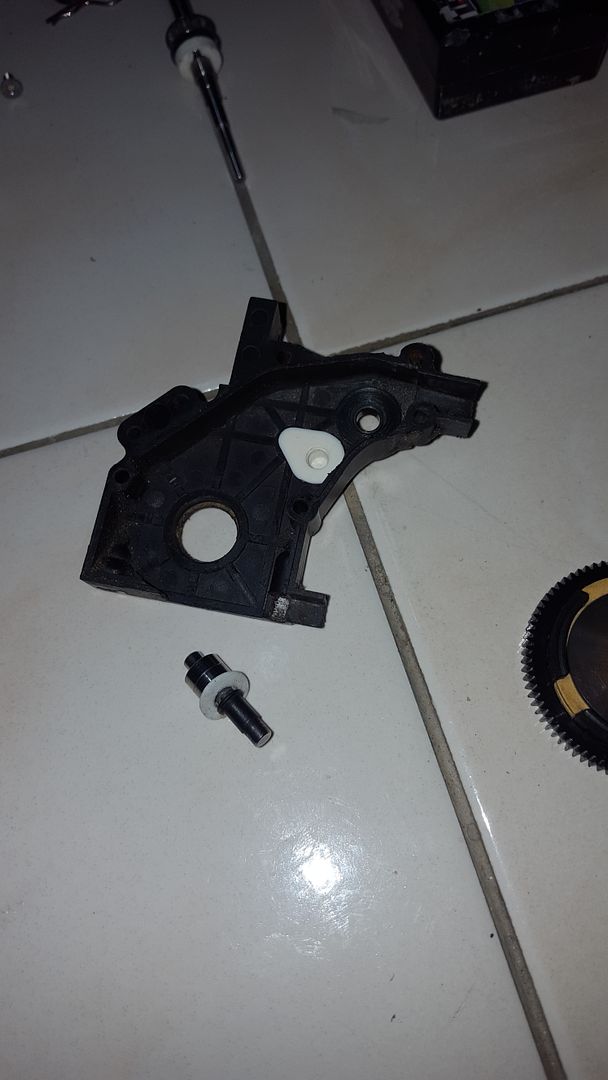
4. How the single short belt looks like assembled.
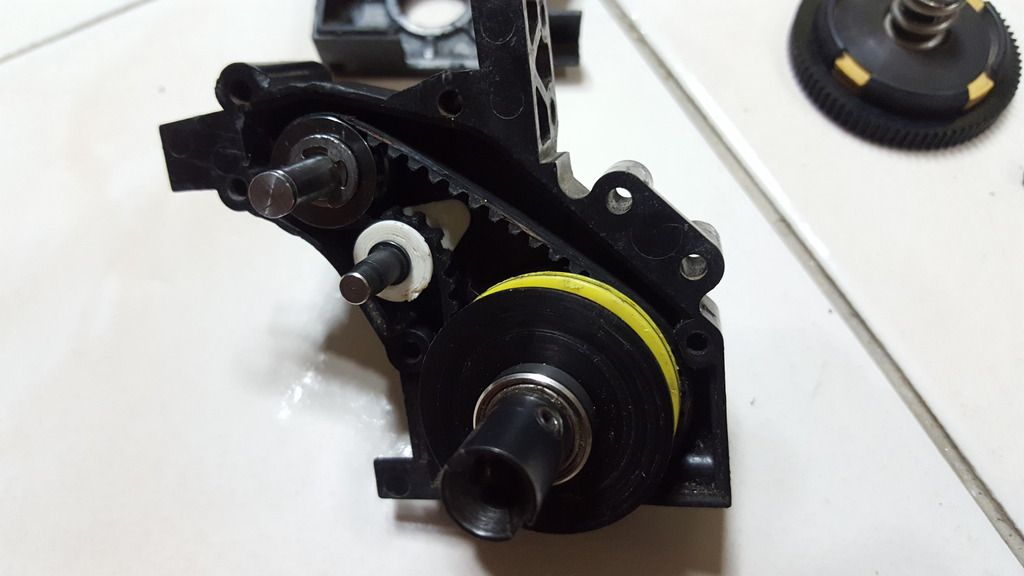
5. How it looks like with both belts.
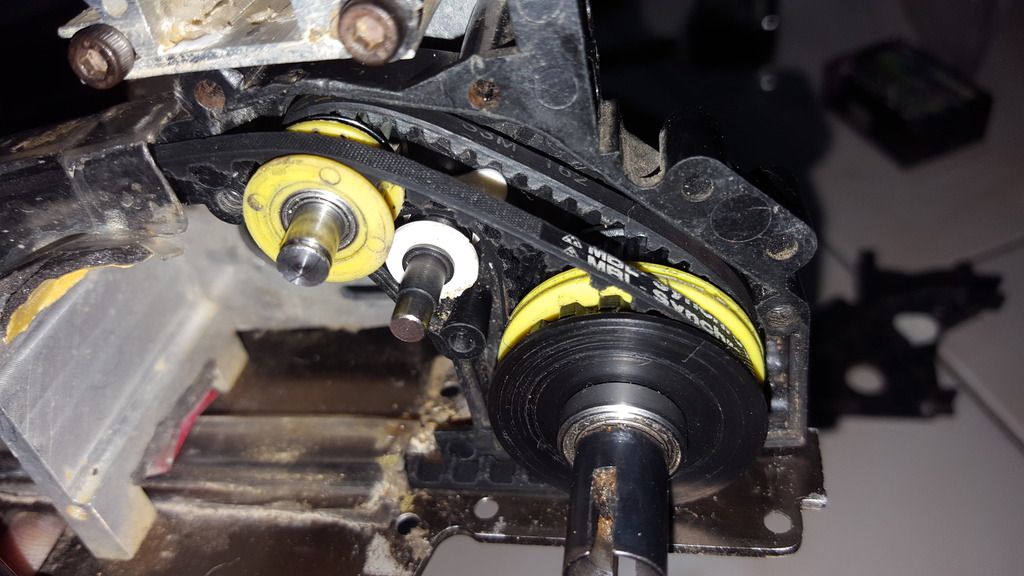
As i said, i had issues with the machined pulley so I revised the dimensions on the pulleys and Got it 3D printed by shapeways.
This are the pulleys i designed, and its compatible with Optima Re re gear diff parts, but internally its same as the Old design gear diffs (no o ring and gasket).
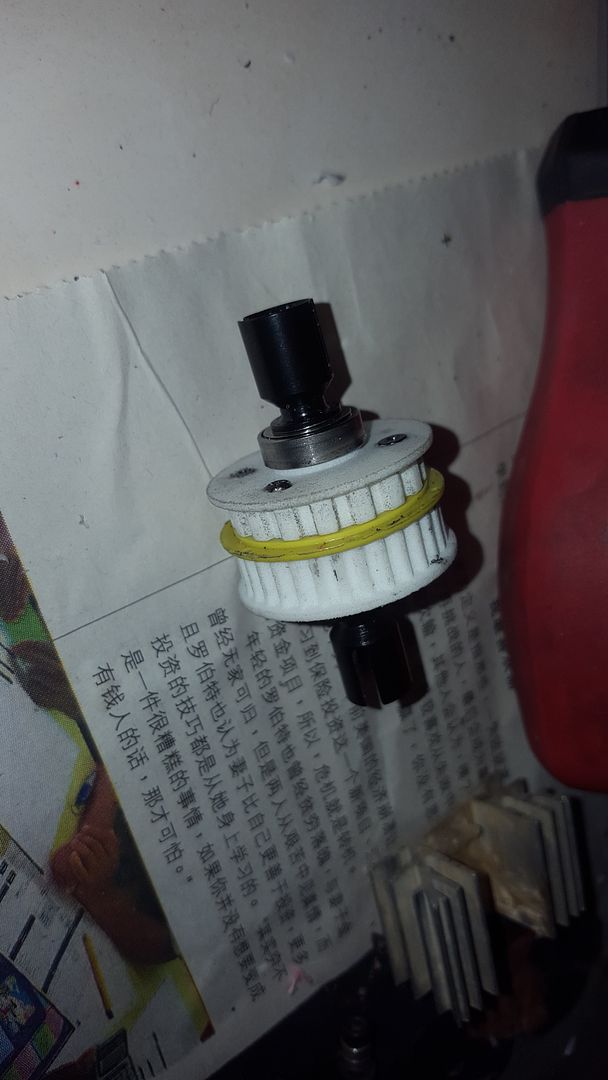
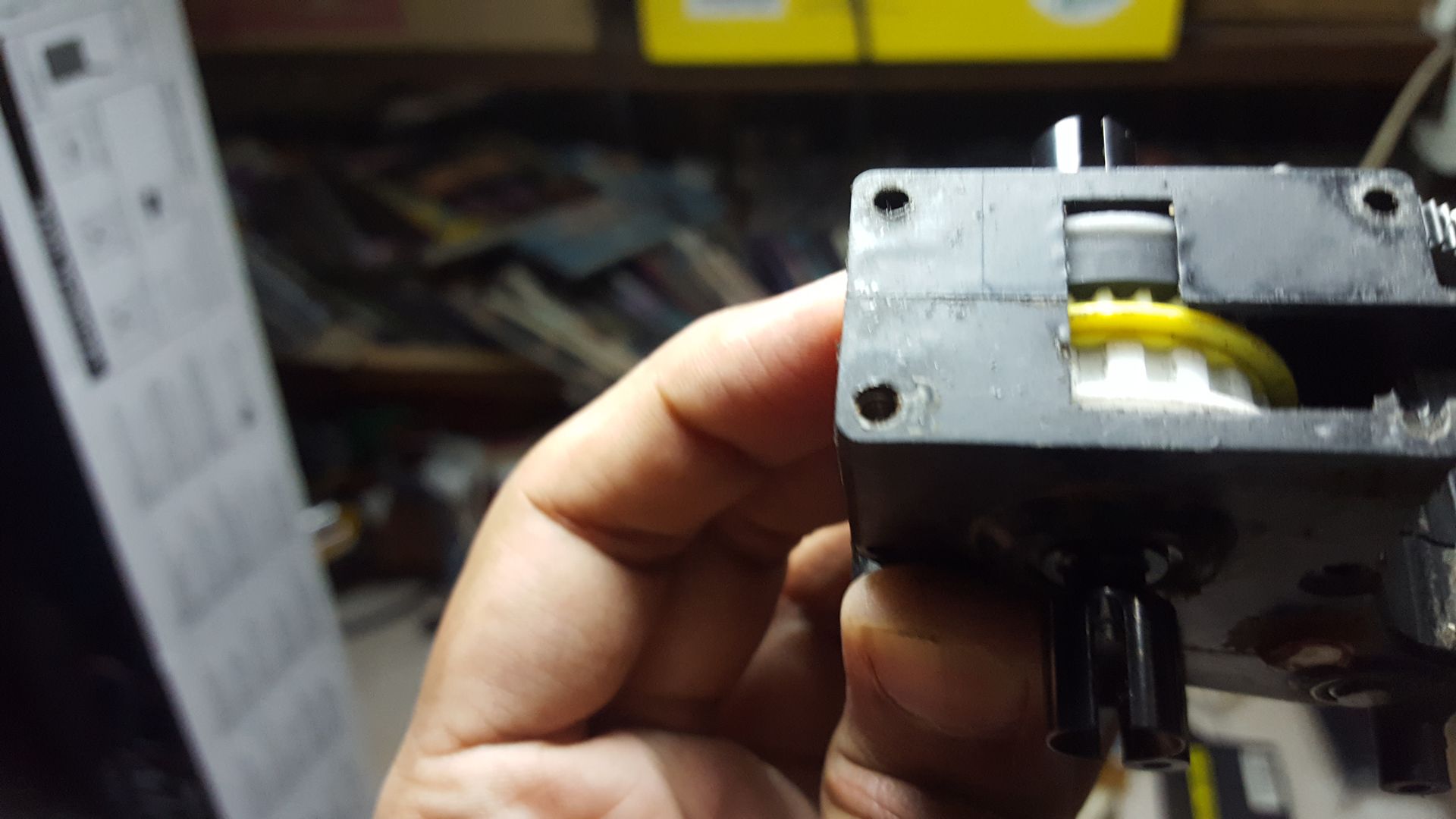
This pic shows the gearbox assembled up.
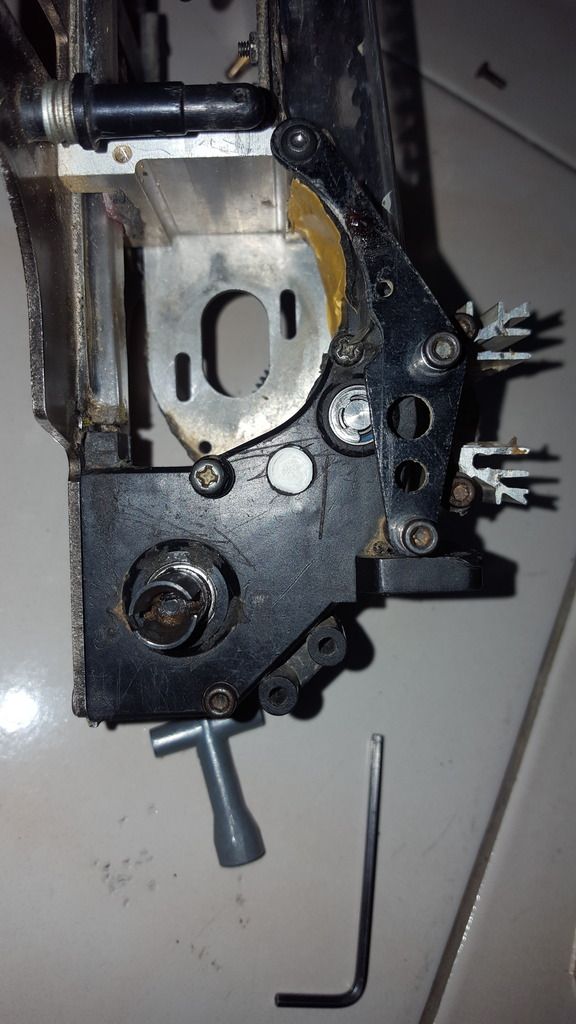
I tested the car in my house last night with the latest pulleys and finally there is no belt skipping sound, even with tight clutch and the front wheel lifting slightly. I will test the car this saturday and if it works good i will go on with a long term test. Oh yes, the internal ratio is now 2.214..same as Lazer ZX.