RC10 Basher CNC
Posted: Fri Apr 01, 2022 9:26 am
Hello friends of the RC10
I'm alway in doubt wether I shoud use my RC10s in bad conditions (dirt, mud, snow, skatepark...). It would be a lot of fun, but it would also be a shame to destroy original parts. So I bought a CNC Machine and I will build some "Basher-RC10"s for my Hobbyroom. Biggest compromise: the chassis. Bending this "pan" is very difficult, so I designed a flat chassis with upper deck. First tries made out of some old aluminium, later maybe anidized, and I will make some of carbon.
Noseplate is milled and then bent. Not so easy ti find the right place to bend it, but the next one will be better. I make cuts, 0.5mm deep with a ball end mill to define the place where it bends.
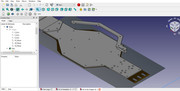
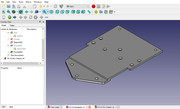
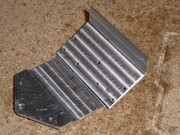
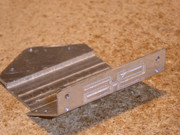
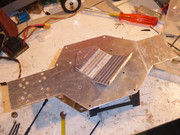
I'm alway in doubt wether I shoud use my RC10s in bad conditions (dirt, mud, snow, skatepark...). It would be a lot of fun, but it would also be a shame to destroy original parts. So I bought a CNC Machine and I will build some "Basher-RC10"s for my Hobbyroom. Biggest compromise: the chassis. Bending this "pan" is very difficult, so I designed a flat chassis with upper deck. First tries made out of some old aluminium, later maybe anidized, and I will make some of carbon.
Noseplate is milled and then bent. Not so easy ti find the right place to bend it, but the next one will be better. I make cuts, 0.5mm deep with a ball end mill to define the place where it bends.
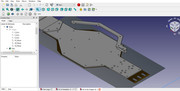
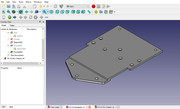
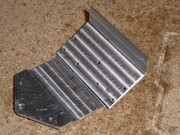
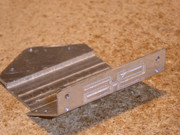
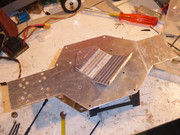